by Jen Hellmann | Mar 19, 2019 | Articles
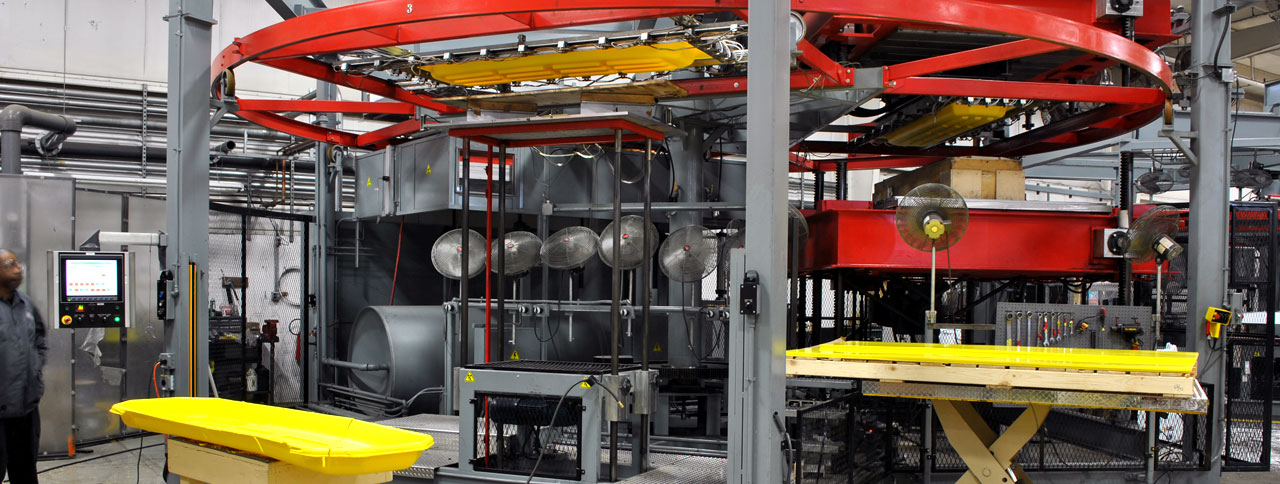
There are many thermoforming materials used in thermoplastics the most familiar are listed below.
ABS
Good general-purpose thermoforming material, very tough yet very hard and rigid, good impact and electrical. Available in gauges from .040 to .475 with several extruded textures. Comes opaque and can be provided in custom colors to match client brands.
ABS/PC
A blend or alloy of ABS and polycarbonate that thermoforms and weathers well, has good color retention, is very hard and has excellent impact.
ABS/PVC
Flame retardant, tough.
Acrylic
Outstanding weather resistance, excellent optics and electrical properties, poor impact, high gloss and deep luster. Available in standard gauges from .080 to over 1″. Available in clear, transparent and opaque colors.
Acrylic, cell cast
Excellent optics and hot strength, more expensive.
Acrylic, continuous and extrusion cast
Large volume use and best price, good optics.
Acrylic film
3 or 6 mil film for laminating, decorating, and weathering of extruded ABS.
DR acrylic
Modified acrylic with higher impact properties.
Acrylic/PVC
A blend of acrylic and PVC that is a tough, chemical-resistant material that weathers well and is flame resistant. Available in custom colors.
HDPE (high-density polyethylene)
Crystalline, very tough materials, good weather resistance with UV inhibitors, resistant to many chemicals. Available in standard gauges from .040 to .500. Available in opaque custom colors. Tough and stiff. Good low temperature. Economical.
HMWPE (high molecular weight)
Excellent environmental stress crack properties, thermoforms well, good low temperature.
HIPS (high impact polystyrene)
Good general-purpose material, rigid. Available in clear but usually opaque custom colors from .030 to .350, low cost.
PVC (vinyl)
Good general-purpose material, good abrasion and chemical resistance. Available in clear but usually opaque custom colors from .030 to .125.
TPO
A great alternative for replacement of composites and comes in several grades that have “paint” like appearance. The melt strength of PP has been modified so you can form deep drawn parts which was very difficult in the infancy of the thermoforming grades.
Expanded PVC
Stiff, light, flat, thermoformable. Available in stock colors and gauges, generally 3 and 6 mm but others are available.
PETG
Clear, higher impact than acrylic, easy to form. Available in gauges from .030 to .500.
Please let us know if you need specific information on materials listed or not listed above. We are here to help!
UV and Paint replacement
For the most part these topics may be discussed in the same conversation.
Most of our materials have high aesthetics for replacing paint and multi-layer extruded product. These materials could be ASA, acrylic or higher-grade substrate material. Multi extruded product allows accomplishing the goal in the most cost-effective method.
Some materials that require UV resistance mainly to avoid color shift rather than promote gloss and/or depth of perception – a UV package is added to the entire substrate as an additive. A good example of this would be HMWPE. This package can range in price and the number of hours (which equates to years) is what drives the cost and minimums. Typically, a 3-5-year package is normal.
Color shift of a material that is protected may range from 1-5 delta E whereas the same product, not protected, may have a shift in the range of 15-25+ delta E. These are generic statements; color, base material and time all affect these results (based on 2500 hours QUV test data). The above is meant to make a general point that the extra cost of adding protection does offer results.
Gloss retention is also an important factor when discussing color shift.
Many of the developments involving paint replacement take in QUV/color shift, gloss retention, depth of image, and scratch and mar resistance. The material suppliers continue to improve their alternatives to the premium of painting a part.
Please contact us for more information on this topic
by Jen Hellmann | Jan 23, 2019 | Articles

Upgrading to thermoforming from metal has many advantages that provide the aesthetics required in today’s market at minimal cost.
There are several benefits for converting metal to a thermoformed part. The four most important (benefits) are:
- Cost
- Weight
- Design Flexibility
- Material advantages
COST
- The more complex the geometry of the part’s design the greater the cost savings. A customer may experience a cost savings of up to 50 percent on a conversion to plastic on a complex part.
- As the part’s complexity and the production volumes increase the advantages of thermoforming grows exponentially. In a metal fabrication, investments in component ancillary tooling may be needed (stamping dies) to achieve shipment releases and cost reductions.
In-direct benefits include:
- Decrease in weight will reduce assembly cost (one assembler rather than two).
- Customer perception of an advanced product due to the flexibility of design and materials available to General Plastics.
WEIGHT
- Thermoforming resins allow engineers to obtain the properties required, while allowing designers the flexibility to achieve the aesthetics required and reduces the cost and weight of the product.
- Depending on the metal alloy, thermoformed plastics may be up to 75 percent lighter based upon specific gravity.
In-direct benefits include:
- Fuel efficiency.
- Decreased emissions.
- Decreased noise and vibration levels.
- Lower overall weight of the product.
- Logistics/freight advantages.
DESIGN FLEXIABILITY
- Ability to produce complex shapes and designs without secondary assembly steps. These same shapes manufactured in metal are expensive and may require ancillary stamping and tooling.
- Ability to form logos and warning labels as well as other branding directly into the part.
- Mating points easily designed in the part.
- Multiple finishes on the same part.
- Part Consolidation.
Indirect benefits include:
- Decreased cost.
- Decreased assembly time.
- Decreased part numbers, carrying costs and inventory.
- Increased aesthetics.
- Part consistencies and repeatability from part-to-part as well as lot-to-lot.
MATERIAL ADVANTAGES
- There are many thermoforming resins available – HIPS, ABS, PC, PE, TPO, acrylic and alloys – the correct material is matched to achieve the clients’ needed requirements and pricing.
- Materials meet flame, smoke and toxicity requirements that are required by the transit industry.
- Monolithic color eliminates painting.
- Texture availability without cost implications on sheet.
- Texture tooling for specific texture requirements.
- No corrosion.
General Plastics, Inc. is your full-service thermoforming solution with more than 30 years of experience with expertise in the following applications:
- Pressure forming (6’ x 10’)
- Vacuum forming (6’ x 10’)
- CNC & Robotic trimming
- Full assembly and sourcing
- Packaging and kitting
- Prototype and production tooling
- DFMA assistance
- Design freedom for undercuts, texture and color
To discuss your Thermoforming needs, call General Plastics, 414-727-6855; Toll Free: (888) 611-0270 or email us sales@genplas.com.
by Jen Hellmann | Nov 7, 2018 | Articles
General Plastics, Inc. is not only located in Milwaukee, Wisconsin, but it is a valuable member of the community, willing to work with others to solve concerns by applying what the company knows best – conceiving problem-solving solutions and producing solutions through thermoforming plastics. Two examples of the company’s recent community work involved the Milwaukee Public Schools (MPS) to solve issues that are not available in the general market-place.
The first project was to create a way to cover the lead filter on every drinking fountain in the MPS system. The manufacturer of the fountains and filter did not have a cover and the MPS master plumber was concerned with the possibility that kids could damage the exposed filter.
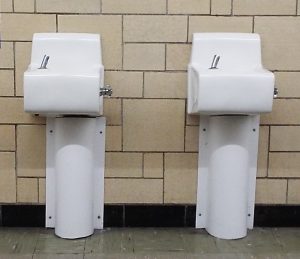
The original intent for this filter was to be installed under a cabinet. MPS provided a steel prototype that General Plastics converted to plastic.
The second project was to help MPS with its issue of having the schools’ digital clocks from being vandalized and destroyed. MPS could not find a cover to protect the clocks on the general market, so General Plastics developed a concept and solution to the problem making covers for the clocks out of plastic.
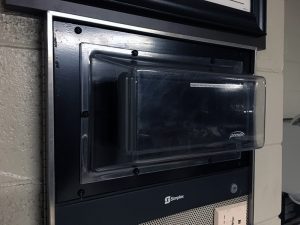
“We believe it is our civic responsibility to get involved and help institutions, such as MPS, in solving serious concerns. As in the case of these two examples, our experience and expertise in plastics was the solution that were not solvable in the general marketplace,” said Bob Porsche, Owner and President, General Plastics, Inc.
General Plastics, Inc. is your full-service thermoforming solution with more than 30 years of experience with expertise in the following applications:
- Pressure forming (6’ x 10’)
- Vacuum forming (6’ x 10’)
- CNC & Robotic trimming
- Full assembly and sourcing
- Packaging and kitting
- Prototype and production tooling
- DFMA assistance
- Design freedom for undercuts, texture and color
To discuss your Thermoforming needs, call General Plastics, 414-727-6855; Toll-Free: (888) 611-0270 or email us sales@genplas.com.
by Jen Hellmann | Aug 24, 2018 | Articles
Last spring, General Plastics hosted a five-hour Leadership Workshop in its Training Center for 60 Brown Deer High School students. The students were members of DECA (previously known as Delta Epsilon Chi and Distributive Education Clubs of America) and other student leadership groups.
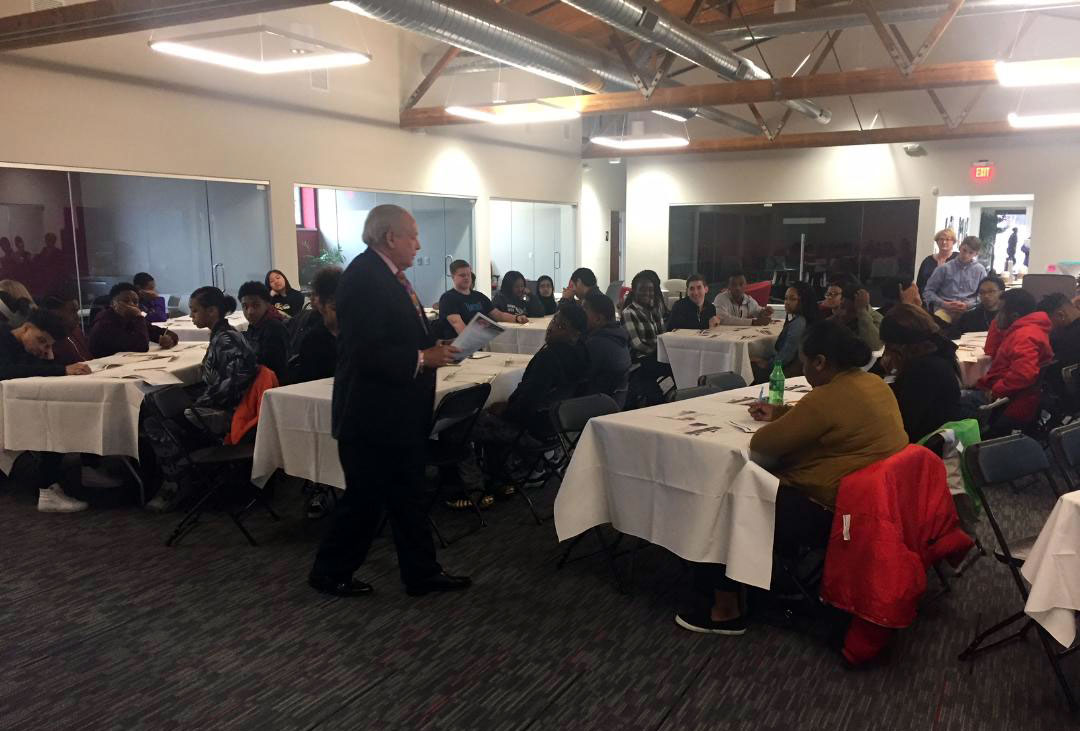
The program, THE TOOLS OF LIFE AND LEADERSHIP, was presented by Chuck Zamora, President of Zamora Group International – The Learning Company and focused on several key leadership skills, including:
- A clear definition of success.
- How to grow your leadership skills.
- The difference between Personal Power and Positional Power.
- Communication is a vital component to achieving success: “Communication – It’s Not Just All Talk”
- Why goals are so important. “If You Don’t Know Where You Are Going, you Might End Up Where You Don’t Want to Be”.
Mr. Zamora is an international speaker, and, to date, has delivered THE TOOLS OF LIFE AND LEADERSHIP to more than 92,000 students on two continents.
According to Bob Porsche, Owner and President, General Plastics, Inc., “The students were an amazing group and interacted well with our guest speaker.” Participants of this and other student training programs offer students good experiences in learning about the plastics industry and expands their future career opportunities.
“General Plastics endeavors to be involved with area schools in the industry and welcomes the opportunity to host similar programs for our community’s future leaders,” said Mr. Porsche.
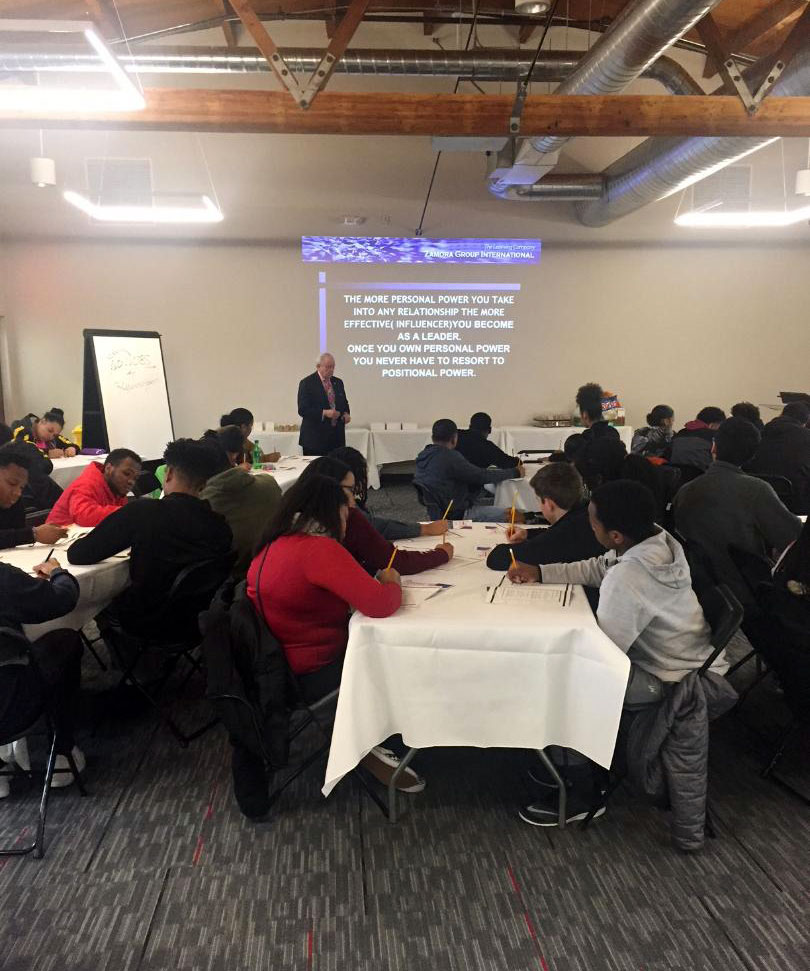
Follow Us!