by Jen Hellmann | Mar 12, 2020 | Articles
General Plastics, Inc. (GP) recently welcomed an additive tooling group to the company’s training center. The group presented their low-cost 3D printed tooling capabilities and discussed their ability to produce low volume production parts in half the time and at half the cost of traditional tooling. Their tools are not water cooled and depending on the geometry of the prototypes involved, may last for approximately 1,000 parts.
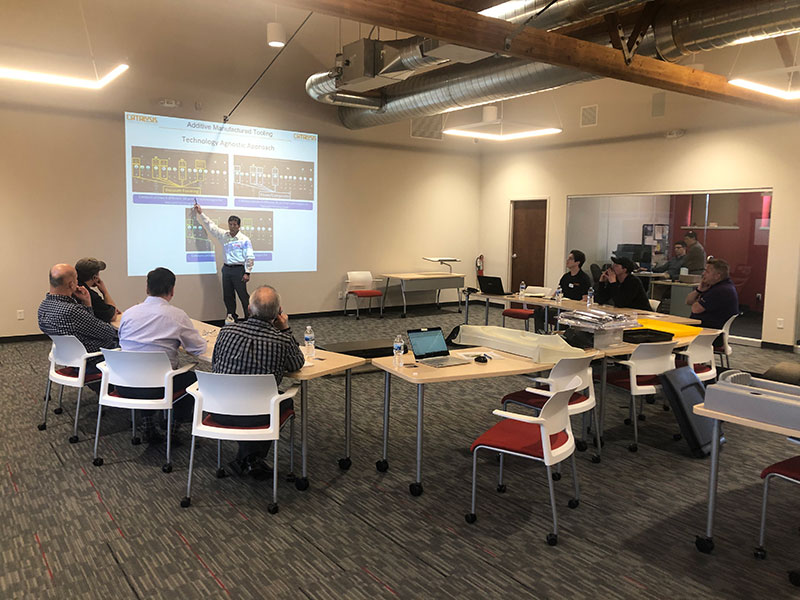
“We welcome new, more economical ways for us to consider in creating prototypes for our customers,” said Bob Porsche, Owner and President, General Plastics, Inc.
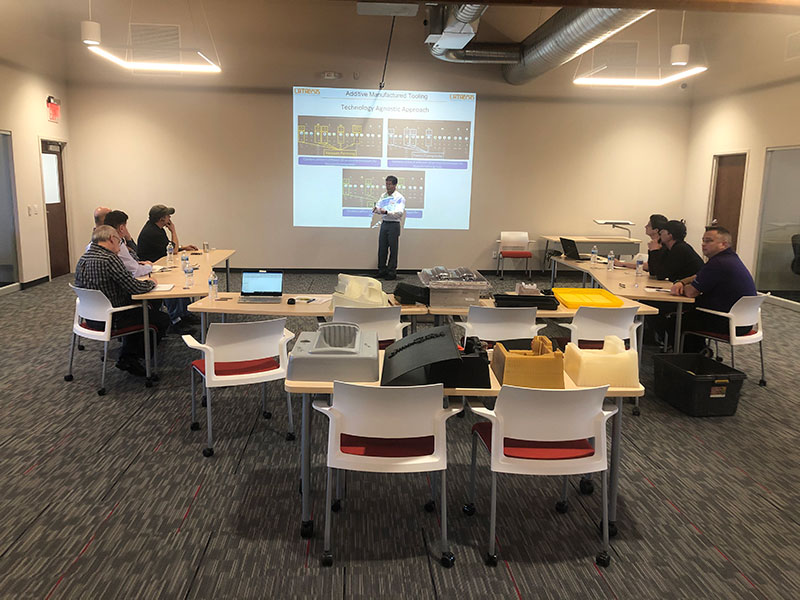
If you would like to learn more about our additive tooling capabilities please contact, sales@genplas.com, or visit our website prototype tooling page, http://www.genplas.com/patterns-prototype-tooling/
ABOUT GENERAL PLASTICS, INC.
General Plastics, Inc. (GP) is an ISO 9001:2015 and (previously) ISO 14001-2004 certified, full service custom plastic thermoformer.
GP provides high quality and cost effective turnkey solutions for Original Equipment Manufacturers (OEM’s) in markets such as Bus, Rail, Truck, Marine, Office, Lavatory, Medical, Health & Wellness, Gaming, Arcade, Food & Beverage, Construction, Machine Guarding and Point of Purchase (POP) throughout the US and Canada.
by Jen Hellmann | Sep 10, 2019 | Articles
This is the second installment of our employee introductions. We are fortunate to have many incredible employees committed to our goal of delivering products that meet industry standards while achieving, or exceeding customer expectations.
Let us introduce…
Jason Bartelt, Program Director
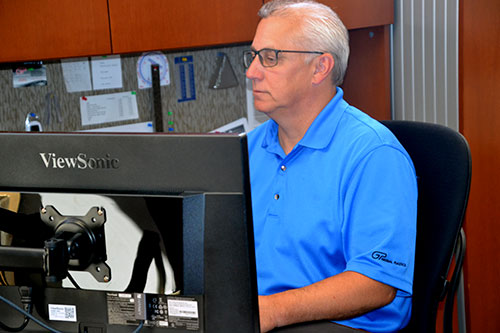
As a Program Director, Jason launches all the new product orders. Upon receiving the files from the customer, he reviews them to make sure the part can be made according to the customer’s specifications. Jason works very closely with the customer’s engineering and design groups and makes suggestions and design changes based on our process while still maintaining the customer’s part concept.
Jason has worked in the manufacturing industry for 31 years starting out in the shop, working his way up. As a result, he’s done pretty much everything that was needed while gaining a familiarity of nearly all departments. There are many aspects, departments and people involved in the launch of a new product and with Jason’s background he understands what is needed and how to take it through the proper channels. For example: if there is assembly involved it will need to include forming the parts and essentially coordinating all departments throughout the shop; if tooling is needed it has to be reviewed by the tooling department, and then scheduled through forming, trimming, programming and quality control for start-up approvals and then shipping.
Just recently the company completed a product launch for a large coach builder. This involved building more than 70 new tools over an eight-month period. He believes it was the largest new product launch in the history of General Plastics. Most of the new products involved assemblies so Jason worked with production, programming, fixturing and assembly to complete the product launch of each tool. It was quite the undertaking and Jason handled it without missing a beat.
Jason has been with General Plastics for five and a half years and in that time, he has enjoyed watching it grow. Over the years, he as seen changes made to improve processes and systems, the workflow, new equipment and technology purchases, etc. – all for the sake of making the company the best it can be. As impressive as the attention to constant improvement is, the owner and management are as attentive to being involved in the company, the employees and the community. Pointing to the many awards such as the 2018 Wisconsin Association of School Boards Business Honor Roll (WASB); the 2017 and 2018 Thermoformer of the Year; the 2014 and 2016 Manufacturer of the Year, 2016 and 2017 Milwaukee’s Future 50 Program award, the 2017 Sustainability Business Process Award from Wisconsin Business Council and more – Jason makes his point – all speak volumes about a small company such as General Plastics committed to the industry and community.
The thing Jason likes best in his position is seeing the customers’ initial concepts work their way through the process to becoming a reality, an actual working part.
Sometimes an order comes in that seems impossible and we initially feel overwhelmed and stressed but then we shake it off and get to work. We realize that we are here to provide a product for the customer and if we can’t do it in their timeframe then we fail and if we fail, they will find someone who will get it done. When we all pull together, work through the order and meet our customers’ needs, I feel like I did my job the way I was supposed to; I think we all feel that way.
Dan Mathieu, Logistics Coordinator
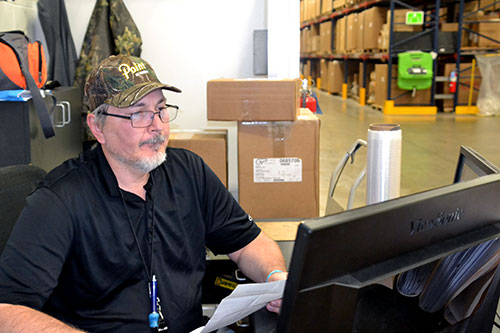
As a Logistics Coordinator Dan coordinates some of the trucks and handles receiving for incoming product. Dan also manages our recycle/trim program and works with suppliers to return trim scrap so it can be put back into sheet form. It takes a lot of coordination to keep everything separate, clean and organized and sent back to the correct suppliers depending on materials.
While he has some college, his studies were not geared toward shipping and receiving and has learned his job mostly from what he’s done on the job. Daniel came to the company 11 years ago and has enjoyed watching it grow. He has seen an increase in the number and types of products they are building and more employees. There is also new and added equipment such as forklifts, rotary machines, CNCs including a robot CNC. In addition, the computer systems are consistently being upgraded.
To do Dan’s job a person needs computer knowledge, forklift driving skills, a willingness to make sure things get done, have attention to detail and be goal oriented. He would add that it is important to show up to make sure the job gets done; he can count on two hands the number of times he has been absent during his 11 years at General Plastics. He started out as a Shipping Clerk, then an Assembly Coordinator and now he is the Logistics Coordinator. According to Daniel, people who want to advance in their position can do so at General Plastics, he is a perfect example.
When he left his former company, he noticed how family-oriented General Plastics was and continues to be. It is not uncommon for employees to see the owner on the floor just saying hi and asking how they’re doing; management is on the floor on a regular basis too. They are friendly and take good care of their employees, offering good benefits including a bonus program and a 401K.
Dan likes working here, and especially enjoys the individuals he works with…
I know I can trust them to get the job done without standing over them to make sure they’re doing it right; we all work together, which makes it less stressful for me and for them – we are a team.
by Jen Hellmann | Jul 9, 2019 | Articles
General Plastics, Inc. can live its slogan, We Form Concept into Reality™ because our leadership leads by example and, in doing so, has inspired our staff; working as a team to form the culture that is needed to deliver products that meet industry standards while achieving, or exceeding customer expectations.
There are many careers within General Plastics and people who are proud to be part of the company, its people, customers and the products we manufacture. Over the next few months we will introduce you to several of them.
Let us Introduce…
Rob Weileder, IT Manager
As the IT Manager, Rob wears many hats. He is the IT department – taking care of all aspects of the technology needs of the organization. He works on several software projects such as rearranging the plant for better workflow; building additions and the remodeling project in the front area. He also designs software programs to make things easier for the people in the plant such as the label printing program. Installing label stations in various locations throughout the plant allows the people on the floor to scan their work order and print the necessary labels. The outcome has increased productivity and quality and reduced (if not eliminated) labeling errors.
The company is ISO 9001 and (previously) ISO 14001 certified. Rob has been involved in the certification projects from the start in helping the company earn and maintain them. He enjoys being involved in the ISO projects and was especially challenged with the ISO-14001, which is an environmental certification. To maintain this certification, he was constantly looking for ways to reduce, recycle or use materials more responsibly and raising awareness throughout the company.
Rob is a right-angle square corner type of guy who can see multiple ways of accomplishing things and determining which is best – if it doesn’t work out as expected there are other approaches, all with the underlining goal of making things easier and more efficient for people and less error prone. He is a methodical thinker with a talent for having an attention for detail; he never knows where the day will take him, but he is always enthusiastic and interested in helping wherever he is needed.
My favorite thing to do is to create efficiencies in everyday workplace settings. One day I’m writing software programs to make someone’s job easier, the next I’m redesigning a machine for a whole different process. From the owner’s computer needs and projects to the guy pushing the button and packing parts, I get to work with everyone.
by Jen Hellmann | Jun 21, 2019 | Articles
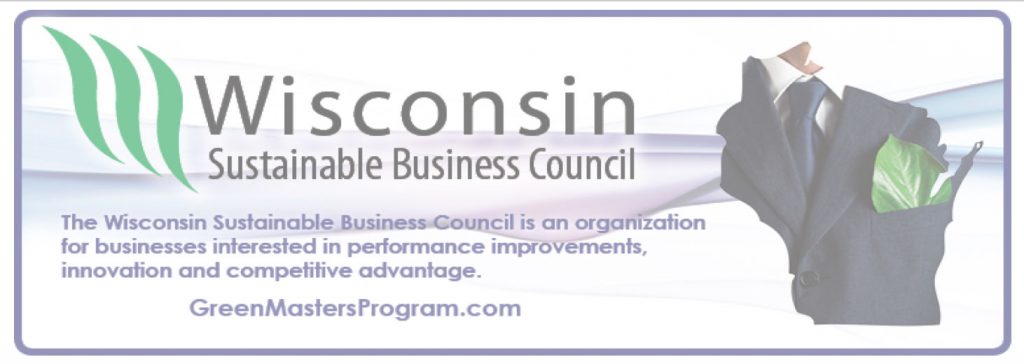
Milwaukee, Wis. (September 2018) – The Wisconsin Sustainable Business Council has named General Plastics Inc.(GP) a Green Professional level company within its Green Masters Program. Recognizing sustainable actions by businesses from across the state of Wisconsin, the Green Masters program works to identify businesses that have taken at least one action within each of the nine pillars of ‘sustainability’. Participants in the program (almost 200 in calendar year 2017) receive recognition for their sustainability accomplishments and develop ideas for future sustainability actions.
General Plastics has been an environmental steward for many years. Since 2010 GP has reduced their dumpster pickups by 50 percent while at the same time almost doubling production and sales. Currently they have been able to recycle or reuse 91.3 percent of their scrap and waste, diverting them from the landfill. Since 2013 General Plastics Inc. has reduced their electricity cost by 31 percent, as a percentage of production dollars. To achieve these results, they focused in multiple different areas: Improving overall equipment efficiency, former oven-zoning improvements to optimize heat profiles, and developed a compressed air leak program. With their 2016/2017 42,000sq.ft. building expansion and office upgrade General Plastics added energy efficient lighting with occupancy sensors, high efficiency windows, insulated walls, and employee training spaces. They have also reduced the overall transportation cost and distance product travels and have worked with several customers to develop reusable packaging options.
GP has strategically made the decision to aggressively grow the business in an environmentally sustainable way. This decision has also increased their growth into new business because their vision, values, and execution aligned well with the market segments and targeted customers. When GP started their environmental journey, the goal was to develop the programs in a profitable, sustainable, easily managed and monitored way. This was so the programs would be a part of the organization for the long haul. This summer (2018) General Plastics brought in a sustainability intern from UW-Madison. Matt Aronson helped to develop an annual company sustainability report, as well as many initiatives this summer. He also gathered the data required to determine our overall carbon footprint.
The Green Masters Program is an objective, points-based recognition and assessment program that enables Wisconsin businesses of all sizes and from any sector to join a group of like-minded companies that are on the road to sustainability. The program has established three levels of participation: Green Apprentice, Green Professional, and Green Master. Each year at the Wisconsin Sustainable Business Conference, the top 20 percent of companies that applied during the calendar year are identified and recognized as the Green Masters level companies for the year.
In 2017 General Plastics won the Sustainable Business Process Award. “General Plastics has implemented creative strategies which define them as a leader in sustainability,” says Kevin Banas, Program Director of the Green Masters Program. “They’ve made going green personal in terms of their strategy. They’ve adopted environmental and social programs that benefit their community, employees, and their customers.”
General Plastics, Inc. (GP) is an ISO 9001 certified and previously 14001 certified, full service custom plastic thermoformer, fabricator, and value-added assembler, located on the north side of Milwaukee, Wisconsin. When Bob Porsche purchased the company in 1987, GP only had 8 full-time employees in an 11,000sq.ft. facility. Currently GP has over 80 dedicated full-time employees and is now a 93,000 sq. ft. building. GP’s mission is to lead the industry in customer connection through support, employee engagement and development, product and process improvement, leading Environment Health & Safety programs (EHS), and to be a steward within the industry and our community. GP is always investigating and investing in the newest technology to ensure that they can support any of their customers current and future needs.
GP provides high quality and cost effective turnkey solutions for Point of Purchase (POP) and Original Equipment Manufacturers (OEM’s) in the following markets: Bus, Rail, Truck, Marine, Office, Lavatory, Medical, Health & Wellness, Gaming, Arcade, Food & Beverage, Agricultural, Construction, and Machine Guarding. The customer base that they service is located throughout the United States and Canada.
The WI Sustainable Business Council is a network of Wisconsin businesses that are leaders in integrating principles of sustainability into business operations. The business case for sustainability (defined in terms of people, planet and profit) has never been stronger. Wisconsin businesses are playing a leadership role in not only ensuring the protection and preservation of our natural resources but in creating a vibrant and growing economy. The Council provides best-in-class sustainability resources and brings businesses together to share knowledge, experiences and tools. Find us on the web at www.wisconsinsustainability.com
by Jen Hellmann | Jun 21, 2019 | Articles
By: APICS Milwaukee Chapter
June 2019
Wednesday June 12, the APICS Milwaukee Breakfast Roundtable Group toured General Plastics, Inc. (GP). GP is an ISO 9001:2015 and (previously) ISO 14001: 2015 certified, full-service custom plastic thermo-former located on the northside of Milwaukee.
Our tour focused on “Sustainability”. GP was certified to the ISO 14001 Environmental Management System Standard and are part of the Green Master’s Program in which they have attained “Green Professional” status.
Our host, Patrick Cain is the plant manager. He discussed with us their processes to keep their employees safe and engaged. Their sustainability program’s goal is to develop programs that are profitable, sustainable and easily managed and monitored. He shared their environmental dashboard and how they track their progress in reducing electricity, water and gas consumption as well as reducing dumpster pick-ups.
GP has developed a “Best Practice” process of recycling plastic by color coding containers by type of plastic and placing that scrap in the color-coded container. This way they can ship back to their suppliers to use in more of their raw materials and get a higher price for their recycling.
There were also many ergonomic improvements that were implemented throughout the site including a vacuum pick up so one person instead of two can move heavy equipment and materials. They have also implemented adjustable tables for better ergonomic workspaces.
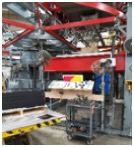
Thank you, GP, for your hospitality and support of the APICS Milwaukee Chapter!
Your APICS Milwaukee Chapter, with approximately 500 members, is a non-profit association with a mission to serve Supply Chain professionals and their companies in the Milwaukee area. We recently added our Fall instructor-led certification classes for CPIM, CSCP and CLTD! Check out our website for more information on how you can advance your career today!

If you are interested in hosting a tour at your company to showcase how you are addressing today’s supply chain challenges, please contact us via our website at: http://apicsmilw.org or via email at: APICS-MILWAUKEE@APICSMILW.ORG.
by Jen Hellmann | Mar 19, 2019 | Articles
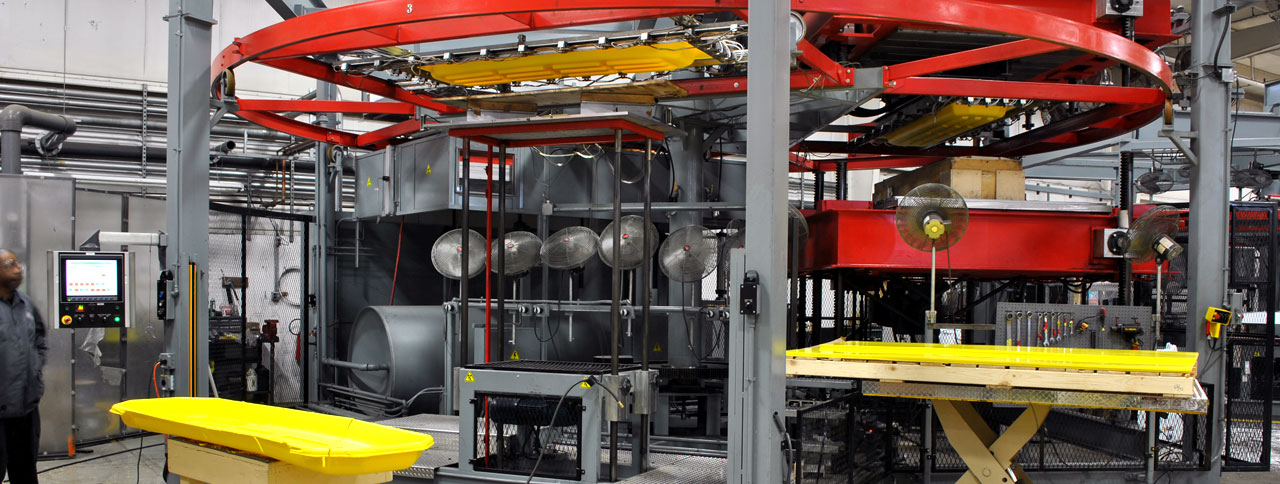
There are many thermoforming materials used in thermoplastics the most familiar are listed below.
ABS
Good general-purpose thermoforming material, very tough yet very hard and rigid, good impact and electrical. Available in gauges from .040 to .475 with several extruded textures. Comes opaque and can be provided in custom colors to match client brands.
ABS/PC
A blend or alloy of ABS and polycarbonate that thermoforms and weathers well, has good color retention, is very hard and has excellent impact.
ABS/PVC
Flame retardant, tough.
Acrylic
Outstanding weather resistance, excellent optics and electrical properties, poor impact, high gloss and deep luster. Available in standard gauges from .080 to over 1″. Available in clear, transparent and opaque colors.
Acrylic, cell cast
Excellent optics and hot strength, more expensive.
Acrylic, continuous and extrusion cast
Large volume use and best price, good optics.
Acrylic film
3 or 6 mil film for laminating, decorating, and weathering of extruded ABS.
DR acrylic
Modified acrylic with higher impact properties.
Acrylic/PVC
A blend of acrylic and PVC that is a tough, chemical-resistant material that weathers well and is flame resistant. Available in custom colors.
HDPE (high-density polyethylene)
Crystalline, very tough materials, good weather resistance with UV inhibitors, resistant to many chemicals. Available in standard gauges from .040 to .500. Available in opaque custom colors. Tough and stiff. Good low temperature. Economical.
HMWPE (high molecular weight)
Excellent environmental stress crack properties, thermoforms well, good low temperature.
HIPS (high impact polystyrene)
Good general-purpose material, rigid. Available in clear but usually opaque custom colors from .030 to .350, low cost.
PVC (vinyl)
Good general-purpose material, good abrasion and chemical resistance. Available in clear but usually opaque custom colors from .030 to .125.
TPO
A great alternative for replacement of composites and comes in several grades that have “paint” like appearance. The melt strength of PP has been modified so you can form deep drawn parts which was very difficult in the infancy of the thermoforming grades.
Expanded PVC
Stiff, light, flat, thermoformable. Available in stock colors and gauges, generally 3 and 6 mm but others are available.
PETG
Clear, higher impact than acrylic, easy to form. Available in gauges from .030 to .500.
Please let us know if you need specific information on materials listed or not listed above. We are here to help!
UV and Paint replacement
For the most part these topics may be discussed in the same conversation.
Most of our materials have high aesthetics for replacing paint and multi-layer extruded product. These materials could be ASA, acrylic or higher-grade substrate material. Multi extruded product allows accomplishing the goal in the most cost-effective method.
Some materials that require UV resistance mainly to avoid color shift rather than promote gloss and/or depth of perception – a UV package is added to the entire substrate as an additive. A good example of this would be HMWPE. This package can range in price and the number of hours (which equates to years) is what drives the cost and minimums. Typically, a 3-5-year package is normal.
Color shift of a material that is protected may range from 1-5 delta E whereas the same product, not protected, may have a shift in the range of 15-25+ delta E. These are generic statements; color, base material and time all affect these results (based on 2500 hours QUV test data). The above is meant to make a general point that the extra cost of adding protection does offer results.
Gloss retention is also an important factor when discussing color shift.
Many of the developments involving paint replacement take in QUV/color shift, gloss retention, depth of image, and scratch and mar resistance. The material suppliers continue to improve their alternatives to the premium of painting a part.
Please contact us for more information on this topic
Follow Us!